Description
Aluminum wave perforated panels have emerged as a popular choice in the construction and design industries, offering a unique combination of visual appeal and practical benefits. These panels, characterized by their undulating shape and perforated surfaces, are transforming the way buildings are designed and experienced. This article explores the features, manufacturing process, applications, and advantages of aluminum wave perforated panels.
The wave – shaped design of these panels adds a dynamic and visually interesting element to any structure. The smooth curves can mimic natural forms such as ocean waves or flowing fabric, creating a sense of movement and fluidity. The perforations, which come in various patterns and sizes, further enhance the aesthetic. They can create captivating light and shadow effects as sunlight or artificial light passes through, adding depth and texture to the surface. For example, in a modern office building’s facade, the wave perforated aluminum panels can reflect and refract light in different ways throughout the day, giving the building a constantly changing and engaging appearance.
One of the significant functional features of aluminum wave perforated panels is their ability to improve acoustic performance. The perforations allow air to pass through, which helps in reducing sound reverberation. When installed in spaces such as auditoriums, concert halls, or open – plan offices, these panels can absorb and scatter sound waves. The wave shape also plays a role in disrupting sound propagation, effectively minimizing noise levels. By combining with appropriate acoustic insulation materials on the backside of the panels, they can achieve excellent noise reduction coefficients (NRC), making the environment more acoustically comfortable.
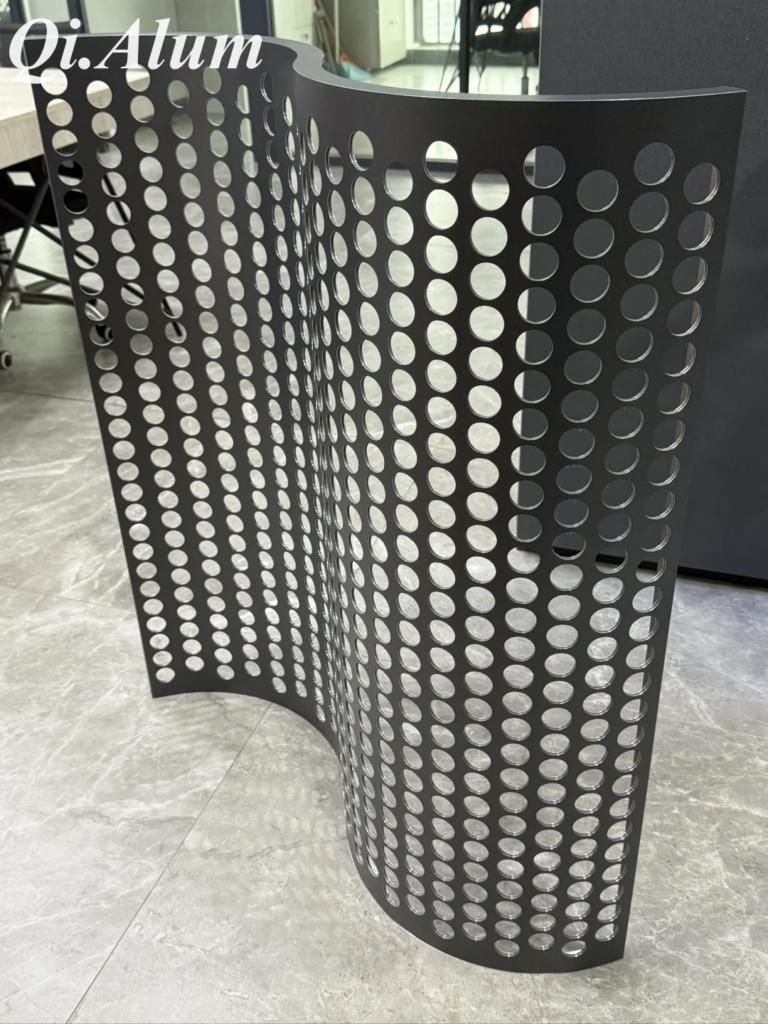
The perforated nature of the panels enables efficient ventilation. In industrial settings like factories or warehouses, they can be used in walls or ceilings to promote air circulation. This is crucial for maintaining a healthy working environment by removing stale air, controlling humidity, and reducing the build – up of heat. In buildings with mechanical ventilation systems, aluminum wave perforated panels can be integrated into the design to act as air diffusers, ensuring a more even distribution of air throughout the space. For example, in a large data center, these panels can help cool the servers by facilitating better airflow around the equipment.
The perforations in the aluminum wave panels allow for a certain degree of light transmission. This can be used to create a semi – transparent effect, which is desirable in many architectural applications. In interior design, they can be used as room dividers or decorative screens, where the light passing through the perforations creates a soft and diffused glow. In exterior applications, such as building facades, the panels can filter sunlight, reducing glare and providing a more comfortable indoor lighting environment. This light – filtering property also contributes to energy efficiency, as it can reduce the need for artificial lighting during the day.
Aluminum wave perforated panels are typically made from high – quality aluminum alloys, such as 3003, 5052, or 6061. Alloy 3003, which contains manganese as the primary alloying element, offers good formability, corrosion resistance, and strength. Alloy 5052, with magnesium as the main alloying element, provides higher strength and excellent corrosion resistance, especially in marine and coastal environments. Alloy 6061, alloyed with magnesium and silicon, is known for its high strength – to – weight ratio and good machinability. The choice of alloy depends on the specific requirements of the application, such as the expected load – bearing capacity, environmental conditions, and aesthetic preferences.
The wave shape is achieved through various forming processes. One common method is roll forming, where a flat aluminum sheet is passed through a series of rollers that gradually shape it into the desired wave profile. This process is efficient for producing large quantities of panels with consistent wave shapes. Another method is press braking, which is more suitable for creating custom – shaped waves or for small – scale production. In press braking, the aluminum sheet is placed in a press and bent into the wave shape using a die. The precision of these forming processes ensures that the wave height, wavelength, and overall shape meet the design specifications.
There are several techniques for creating perforations in the aluminum panels. CNC (Computer Numerical Control) punching is a widely used method, where a computer – controlled punch press creates holes of various shapes (such as round, square, or hexagonal) and sizes in the panel. This method allows for high – precision perforation, with accurate control over the hole pattern and spacing. Laser cutting is another option, especially for creating complex or irregular perforation patterns. Laser cutting uses a high – energy laser beam to melt or vaporize the aluminum, resulting in clean and precise cuts. The choice between CNC punching and laser cutting depends on factors such as the complexity of the pattern, the quantity of panels, and the cost – effectiveness.
After the panels are formed and perforated, they undergo surface treatment to enhance their durability and appearance. Anodizing is a common surface treatment for aluminum wave perforated panels. In this process, an oxide layer is formed on the surface of the aluminum through an electrochemical reaction. The anodized layer provides increased corrosion resistance and can be dyed in a variety of colors to match the design scheme. Another popular surface treatment is powder coating, where a dry powder is electrostatically applied to the panel and then cured in an oven. Powder coating offers a wide range of color options, excellent durability, and good resistance to scratches and abrasions. In some cases, a combination of anodizing and powder coating may be used to achieve the desired performance and aesthetic characteristics.
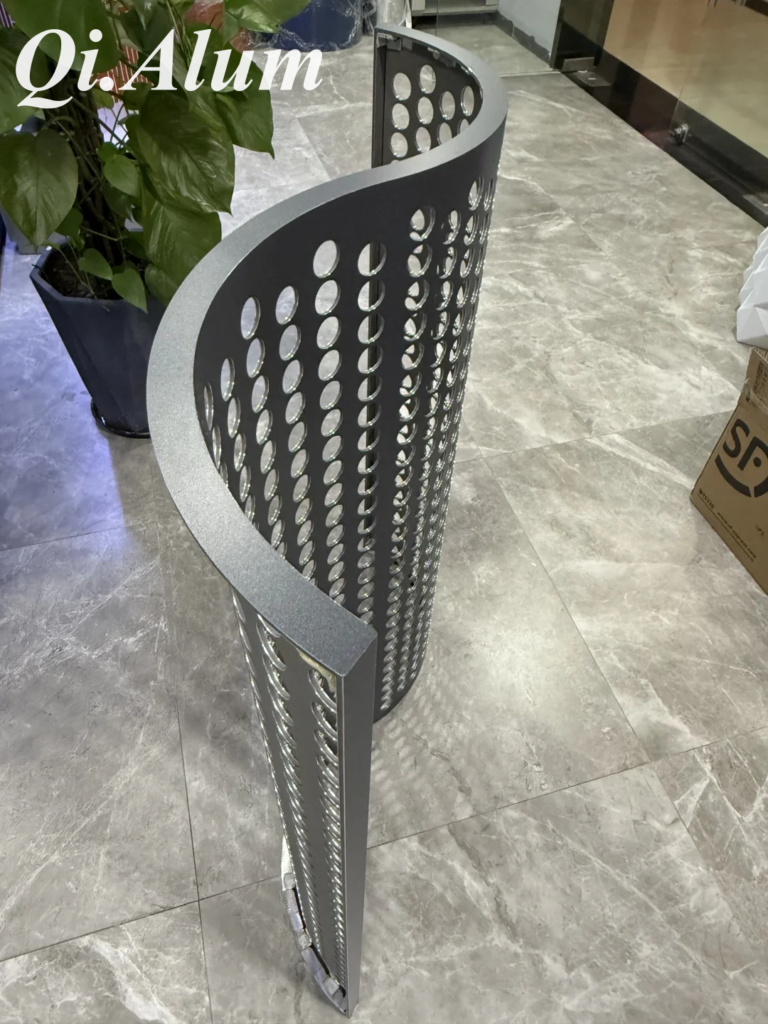
Aluminum wave perforated panels are extensively used in architectural facades to create visually stunning and functional building exteriors. They can be used as a primary cladding material or in combination with other materials such as glass, stone, or concrete. In modern and contemporary architecture, the panels’ unique shape and perforation patterns can convey a sense of innovation and style. For example, in a high – rise building in a city center, the wave perforated aluminum facade can make the building stand out from the surrounding structures, while also providing benefits such as sun shading, ventilation, and acoustic control. The panels can be customized to fit the specific design concept of the building, whether it’s a sleek and minimalist look or a more elaborate and decorative design.
In interior design, aluminum wave perforated panels have a wide range of applications. They can be used as room dividers, adding a touch of elegance and functionality to the space. The perforations allow for visual connection between different areas while still providing a sense of separation. In commercial spaces such as hotels, restaurants, and retail stores, these panels can be used to create focal points or to enhance the overall decor. For example, in a hotel lobby, a large – scale wave perforated aluminum screen can serve as a dramatic entrance feature. In offices, they can be used as acoustic baffles on ceilings or walls to reduce noise levels and improve the working environment. The panels can also be used in interior lighting fixtures, where the perforations can create interesting light patterns.
Industrial and commercial buildings also benefit from the use of aluminum wave perforated panels. In factories, warehouses, and industrial plants, the panels can be used for ventilation systems, allowing for the efficient exchange of air. They can also be used as safety guards around machinery, as the perforated design provides visibility while still protecting workers from moving parts. In commercial buildings such as shopping malls and airports, the panels can be used in ceilings or facades to improve acoustic performance and ventilation. For example, in an airport terminal, the wave perforated aluminum ceiling panels can help reduce the noise from aircraft engines and passenger traffic, while also providing a modern and attractive look.
Outdoor structures such as pergolas, pavilions, and fences can be enhanced with aluminum wave perforated panels. These panels can provide shade, protection from the elements, and a decorative element to outdoor spaces. In a garden pergola, the wave perforated aluminum panels can be used as a roof, allowing for filtered sunlight to enter while protecting from rain. In a public park, aluminum wave perforated fences can be used to create boundaries while still maintaining an open and inviting look. The corrosion resistance of aluminum makes these panels suitable for long – term outdoor use, even in harsh environmental conditions.
Aluminum is a lightweight metal, and aluminum wave perforated panels inherit this property. Compared to traditional building materials such as steel or concrete, aluminum panels are much lighter, which makes them easier to handle and install. In high – rise buildings, the use of lightweight aluminum panels can reduce the overall weight of the structure, leading to cost savings in foundation construction and structural support. The lightweight nature of the panels also makes them suitable for applications where weight is a critical factor, such as in renovating existing buildings with limited load – bearing capacity.
Aluminum is highly durable and resistant to corrosion. The natural oxide layer that forms on the surface of aluminum protects it from rust and degradation. Through surface treatments such as anodizing or powder coating, the durability of aluminum wave perforated panels can be further enhanced. These panels can withstand harsh environmental conditions, including exposure to sunlight, rain, snow, and temperature fluctuations, without significant deterioration. In contrast, traditional materials like wood may rot, warp, or be damaged by insects over time, and steel may rust in the presence of moisture.
Although the initial cost of aluminum wave perforated panels may be higher than some traditional materials, their long – term cost – effectiveness is significant. Their durability means that they require less maintenance and replacement over their lifespan, resulting in lower overall costs. The lightweight nature of the panels also reduces installation costs, as less labor and equipment are needed for handling and installation. Additionally, the energy – efficient properties of the panels, such as their ability to provide natural ventilation and light diffusion, can lead to savings in heating, cooling, and lighting costs in buildings.
Aluminum wave perforated panels offer unparalleled design flexibility. The wave shape can be customized in terms of wave height, wavelength, and amplitude to suit different design concepts. The perforation patterns can also be tailored, with a wide variety of hole shapes, sizes, and arrangements available. This allows architects and designers to create unique and personalized designs that meet the specific aesthetic and functional requirements of each project. In comparison, traditional materials may have more limited design options, especially when it comes to creating complex shapes and patterns.
Aluminum wave perforated panels represent a remarkable advancement in building materials. Their combination of aesthetic appeal, acoustic performance, ventilation capabilities, and light – related properties, along with their lightweight, durability, cost – effectiveness, and design flexibility, make them an ideal choice for a wide range of applications in architecture, interior design, and industrial settings. As the construction and design industries continue to evolve, demanding more innovative and sustainable solutions, aluminum wave perforated panels are likely to play an increasingly important role in shaping the built environment. Whether it’s creating a visually striking building facade, enhancing the functionality of an interior space, or improving the performance of an industrial facility, these panels offer a versatile and reliable option for designers and builders alike.
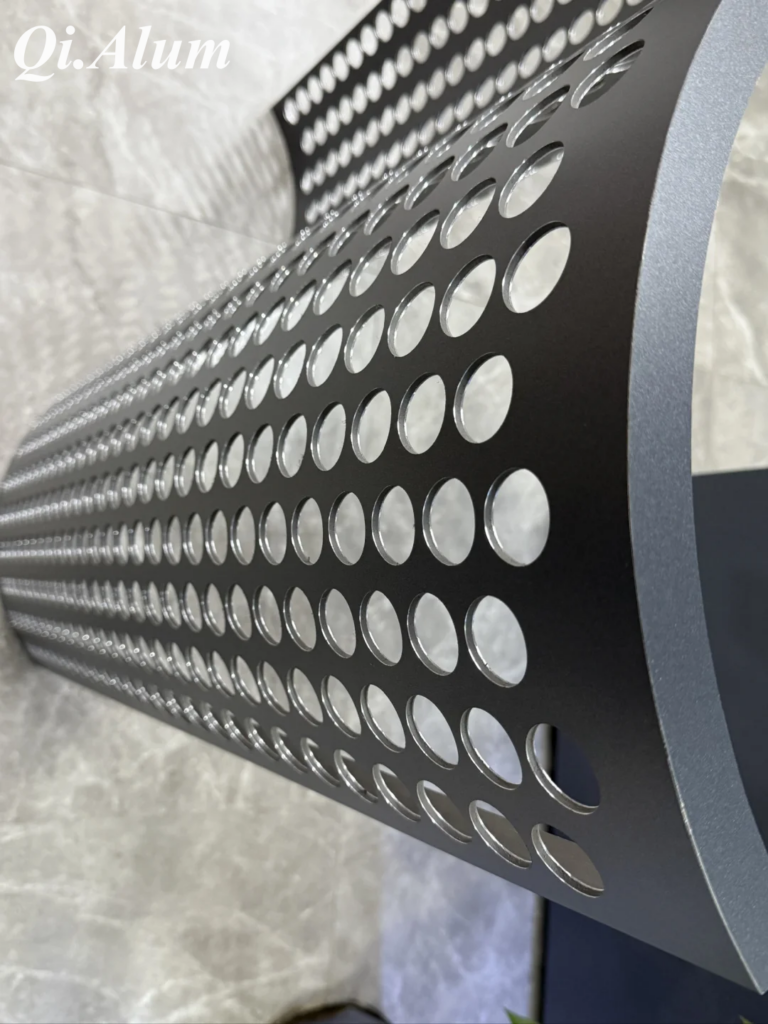
FAQ:
Q:How about customized?
A:Our professional R&D team can meet your OEM/ODM requirement.
Q: How about your quality guarantee ?
A: For all our products, we have certificate and product quality test report.If there is any lost caused by us, we will make compensation.
Q : How about sample ?
A : Free sample can be sent within 5 days after confirmation. But shipping cost will be afford by the buyer, it will be refund when order.
Q : Do you have any successful customer example?
A : Yes, please contact us for more details. And the supplier of Asian City in Guangzhou and Guangzhou Baiyun Airport.
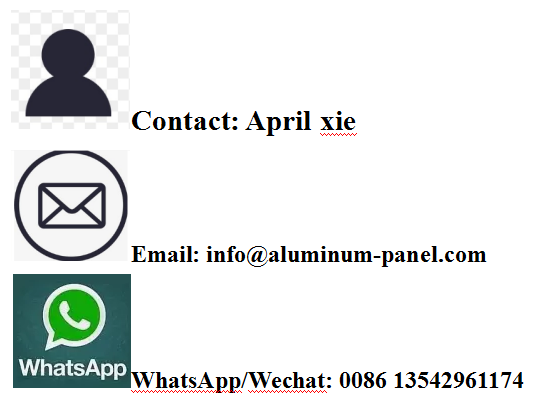
About us:
Foshan Qi Aluminum Decorative Materials Co.,Ltd, more than 12 years experience. We are manufacturer of fabricating aluminum perforated sheets, aluminum solid panels, aluminum screen,aluminum facade decorative sheets, aluminum expanded mesh, aluminum ceiling with good quality and fast delivery for more than 10 years to export countries. Our monthly supplying is about 80000 sqms for inside and outside market. Our projects covers five star hotel, high end villas, school, campus, metro station, airport, office building, shopping mall and some other goverment projects. We can provide design, fabrication and installation one stop service for your projects. High precision, quality guarantee, affordable price, globla delivery and considerate service is our basis. We accept OEM/ODM business. We are the experienced specialist on facade solution decoration!!!
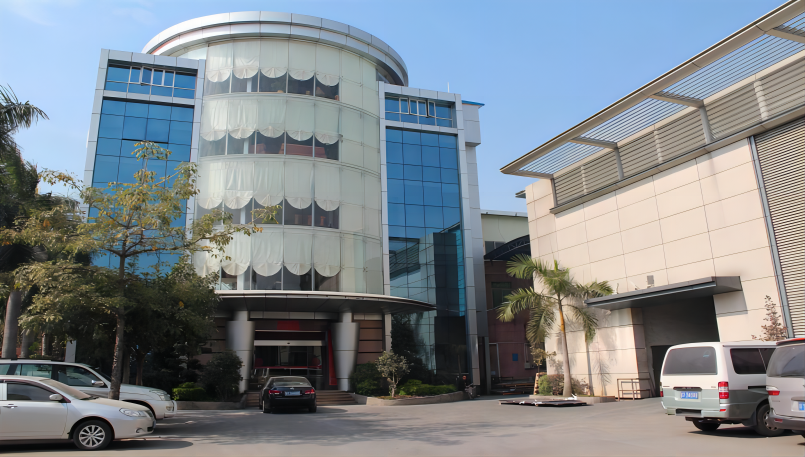