In order to meet the needs of users, decorative aluminum plate through the surface treatment in general to put on the market, so the decorative aluminum surface treatment is more important, how to install decorative aluminum, how to protect the surface of decorative aluminum? Xiaobian talk about decorative aluminum surface treatment methods.
Decorative aluminum surface protection method, no more than three kinds of current:
(1) anodizing, the 1950s has been the introduction of aluminum doors and windows, aluminum doors and windows are still decorated with aluminum and other commonly used surface treatment measures;
(2) anodized after electrophoresis acrylic resin, Japan in the 20th century, 60 years has been commercialized, Europe to the 1970s began to use, is also mainly used in the Asian region. The technology has been developed from transparent bright film to matt and transparent film and color film, the variety is more diversified, industrial control and product quality are relatively stable;
(3) electrostatic treatment after electrostatic spraying, including electrostatic powder coating and electrostatic liquid spray, electrostatic liquid spray fluorocarbon resin in the 20th century, 60 years, the United States has achieved commercialization. The electrostatic powder coating thermosetting polyester coating, the late 60s in Europe has been commercialized, the current European countries still dominate the surface treatment means. Today, a single anodized aluminum doors and windows in domestic and foreign markets were significantly reduced Japan favored in the electrophoretic coating, white electrophoretic coating developed rapidly and applied in Europe. Electrostatic powder coating with its colorful, easy to control, environmental protection, excellent performance and other reasons, has become Europe and the United States preferred surface treatment methods. In recent years, electrostatic powder coating market in China is also rapidly expanding.
(4) paint: usually fluorocarbon spray, aluminum paint before the treatment is more important, to be passivation treatment to ensure that the paint and aluminum plate closely, the typical use of the curtain wall aluminum are used in this way for surface treatment. Whether it is aluminum or aluminum alloy material, which is very important process is the surface treatment. Today to introduce the current more mainstream aluminum surface treatment process. One: electrophoretic paint. Aluminum plate after such treatment, the material surface of the smooth side, while corrosion resistance will be greatly enhanced. Second: powder electrostatic spraying. This process is characterized by enhanced corrosion resistance of aluminum, and for some acid and alkali salt, the use of aluminum sheet is better than the oxidation of colored profiles. Three: multi-tone surface treatment. The moment in order to make aluminum with better use, naturally there have been a variety of color processing, so that the color of aluminum can become more perfect. The last one is the plasma enhanced electrochemical surface of the ceramic. This is the use of advanced science and technology. After this treatment of aluminum quality is excellent, but the cost is relatively high. 1, aluminum and aluminum alloy sheet with hot-rolled state, annealed state, various levels of soft state and a variety of heat treatment state supply aluminum.
2, hot rolling before the preparation, including ingot quality inspection, soaking, sawing, milling, aluminum and heating.
3, semi-continuous casting when the cooling rate is very high, the diffusion process in solid phase is difficult, the ingot is easy to form internal chemical composition and uneven organization, such as intra-crystal segregation, so that plastic
4, the surface of the ingot segregation problems, slag, scarring and cracks and other defects should be milling (see non-ferrous metal alloy ingot milling surface), which is to ensure good quality of the finished product is an important factor
5, hot-rolled: aluminum alloy ingot hot rolling is to provide blank for cold rolling, or direct production of hot-rolled plate.
6, hot rolling process system, including pass down rate, rolling temperature, rolling speed and lubrication cooling, etc.
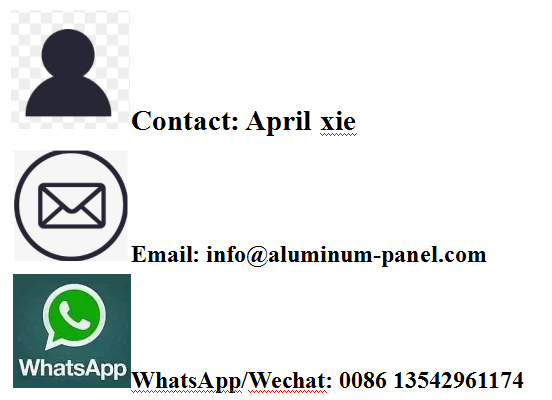