The processing process of aluminum profile mainly includes three steps: casting, extrusion and surface treatment. The surface treatment of aluminum profile is one of the most important links in the processing of aluminum profile, and also the most intuitive inspection items in the acceptance of products. At present, aluminum profile surface treatment technology mainly includes five categories, electrostatic powder spraying, fluorocarbon spraying, electrophoresis, anodic oxidation and wood grain transfer processing. Qi Alum. has more than aluminum profile processing to explain the following 5 different surface treatment technologies and their advantages and disadvantages.
1、electrostatic powder spraying
Principle of electrostatic powder spraying process
The powder coating is sprayed to the surface of the workpiece with electrostatic spraying equipment. Under the action of electrostatic, the powder will be evenly adsorbed on the surface of the workpiece, forming the powdery coating. The powdery coating is baked and solidified at high temperature, and becomes the final coating with different effects.
Electrostatic powder spraying process
Surface pretreatment – spraying – baking curing
Advantages and disadvantages of electrostatic powder spraying
Advantages are less pollution: no organic solvent volatilization in electrostatic powder spraying process, no toluene, dibenzene and other harmful gases in paint coating. Energy saving Electrostatic powder spraying can reduce energy consumption by about 30% due to its one-time film formation. Color selection, according to customer requirements to make a variety of colors, and produce small color difference. Good film performance, one time film thickness up to 50-80μm, good surface adhesion, corrosion resistance
The disadvantage is that the surface treatment of the profile surface is easy to produce orange peel, or even powder, bright color color.
2、fluorocarbon spraying
Fluorocarbon spraying process principle
Fluorocarbon spraying is also a kind of electrostatic spraying, belongs to the way of liquid spraying. Fluorocarbon spray coating is made of polyvinylidene fluoride resin baking as the base material or metal aluminum powder as the color material. There are suspension and semi-suspension, suspension is the pre-treatment and spraying of aluminum, the curing process will be aluminum suspension. Excellent quality fluorocarbon coating has metallic luster, bright color, obvious three-dimensional sense.
Fluorocarbon spraying process
Surface pretreatment – spraying – multi-layer spraying – curing treatment
Advantages and disadvantages of fluorocarbon spraying
Excellent corrosion resistance, thanks to excellent chemical inertness, acid, alkali, salt and other chemical substances and a variety of chemical solvents, to provide a protective barrier for the base material; Fluorocarbon spraying has high surface hardness, impact resistance, buckling resistance and good wear resistance, showing excellent physical and mechanical properties.
Maintenance-free, self-cleaning, fluorocarbon coating has very low surface energy, surface dust can be self-cleaned by rain, excellent hydrophobicity (maximum water absorption rate is less than 5%) and oil repellent, minimal friction coefficient (0.15-0.17), will not stick dust scale, good antifouling
Strong adhesion – in copper, stainless steel and other metals, polyester, polyurethane, vinyl chloride and other plastics, cement, composite materials and other surfaces have its excellent adhesion, in 60 degree gloss meter, can achieve more than 80% of the high gloss.
Ultra long weather resistance – coating contains a large number of F- C bonds, determines its super stability, no powder, do not fade, the service life of up to 20 years, with more excellent performance than any other coating. Excellent construction – long storage period, convenient construction.
The disadvantage is that due to its chemical properties easy to produce volatile substances, light retention, hardness slightly weak.
3、the electric swimming
Working Principle of electrophoresis
Electrophoresis is the electrophoretic coating in the Yin and Yang poles, under the action of voltage, charged coating ions move to the cathode and the alkaline effect of the cathode surface to form insoluble substances, deposited on the surface of the workpiece. Aluminum profile electrophoresis is a process in which the extruded aluminum alloy is placed in the electrophoresis tank and a dense resin film is formed on the surface by direct current. Electrophoretic aluminum profiles are very bright and mirror like, which also improves corrosion resistance.
Electrophoresis workflow
Ultrasonic degreasing – washing – skin film -ED- drying
Advantages and disadvantages of electrophoresis
Advantages are low cost, good protection of the workpiece, because no matter how complex the workpiece can be evenly on the film. And the leveling is good. You can take advantage of these advantages of electrophoresis to mimic the gold and bronze effect of electroplating.
The disadvantage is that the initial investment is relatively large, per kilogram electrophoresis coating is much more expensive than spray paint.
4、anodic oxidation
Working principle of anodic oxidation
Anodized aluminum profile refers to the process in which aluminum and its alloy form an oxide film on aluminum products (anode) under the action of impressed current under the corresponding electrolyte and specific process conditions. But anodic alumina surface formed by the oxide film is different from the general oxide film, anodic alumina can be stained by electrolytic coloring.
5、transfer wood grain
Working principle of wood grain transfer printing
Wood grain transfer profile refers to the powder coating or electrophoretic paint on the basis of high temperature ascension heat penetration principle, through heating, pressure, will transfer paper or transfer film on the wood grain pattern, rapid transfer and penetration into the coating or electrophoretic good profile. So that the production of wood grain profile texture clear, three-dimensional sense of strong, more can reflect the natural feeling of wood grain, is the ideal energy saving and environmental protection material to replace the traditional wood.
Wood grain transfer printing workflow
The processed profile is sprayed with surface background color.
Select customized wood grain paper to transfer the aluminum, sheet metal wrapped, with high temperature adhesive paper fixed paper interface, prevent the wood grain paper loose.
Cover it with a tubular plastic bag with high temperature resistance and good sealing performance, and then vacuum it from both ends of the plastic bag until the plastic bag can fully and effectively stick to the base material.
The wood grain paper wrapped aluminum, sheet metal for baking, baking temperature and the length of time should be based on the characteristics of the substrate and to transfer the surface texture of the depth of comprehensive factors to adjust.
Remove the baking materials, tear off the heat transfer paper, do surface cleaning.
Advantages and disadvantages of wood grain transfer
Environmental protection, so that aluminum products with wood texture, simulation effect is good, instead of wood decorative materials, more energy saving and environmental protection. The printed texture has a strong adhesive effect on aluminum materials, without any taste and zero pollution. It is an environmentally friendly building material.
Wood grain transfer used in aluminum materials, easy to clean. The surface is stained with stains and can be restored to its original appearance after scrubbing with water. Fire resistance, corrosion resistance, moisture resistance, hardness are better than solid wood.
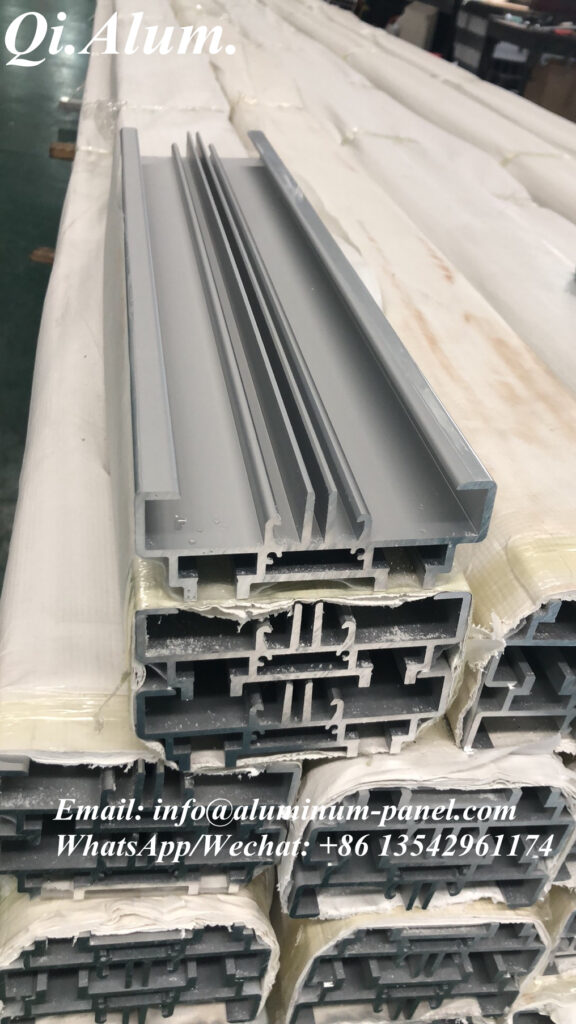

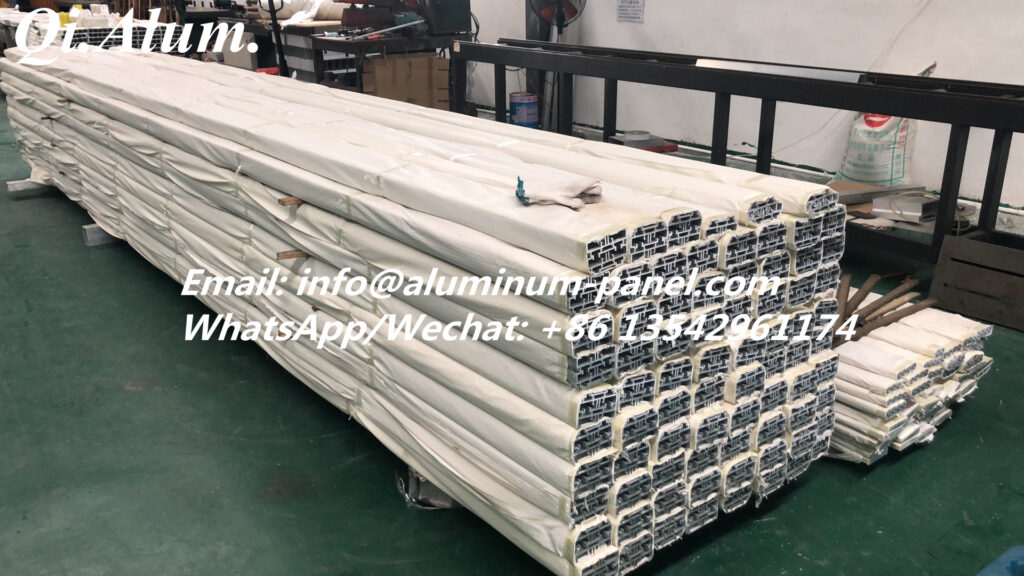