Description
- Problem Description: Incomplete penetration occurs when the weld metal fails to fully fuse with the base metal of the keel framework during the welding process. This can lead to a significant reduction in the joint’s strength and integrity, posing a potential risk to the stability of the entire exterior wall cladding system.
- Solutions: Ensure that the welding surface of the keel is clean and free of rust, oil, and other contaminants before welding. Select the appropriate welding parameters, including welding current, voltage, and welding speed, according to the thickness and material of the keel. For thicker keel materials, consider using multi-layer welding techniques to ensure full penetration.
- Problem Description: Weld porosity refers to the presence of gas bubbles or voids within the weld bead. These pores can weaken the weld, reducing its load-bearing capacity and making it more susceptible to corrosion.
- Solutions: Use welding consumables that are properly stored and free from moisture. During the welding process, maintain a stable arc and appropriate gas shielding (if applicable) to prevent the ingress of air into the weld pool. Control the welding speed to allow sufficient time for gas to escape from the molten metal.
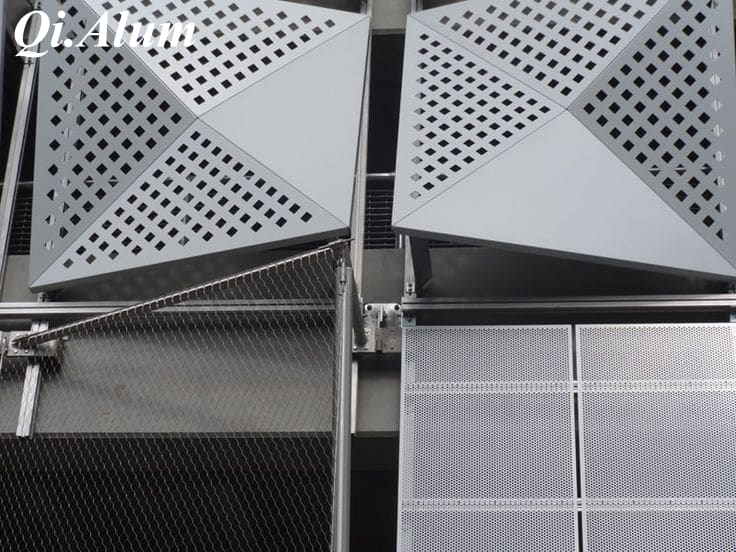
- Problem Description: Weld cracks can be either hot cracks, which occur during the solidification of the weld metal, or cold cracks, which develop after the weld has cooled. Cracks can severely compromise the structural integrity of the keel framework and may lead to the failure of the entire aluminum single panel cladding system.
- Solutions: Select welding materials with a chemical composition that is compatible with the base metal to minimize the risk of cracking. Preheat the keel before welding, especially for materials that are prone to cracking, to reduce the cooling rate of the weld. After welding, perform post-weld heat treatment to relieve residual stresses and improve the ductility of the weld.
- Problem Description: Undercutting is the removal of base metal at the toe of the weld bead, creating a groove or notch. This can reduce the cross-sectional area of the keel, weakening its strength and potentially causing stress concentrations.
- Solutions: Adjust the welding parameters, such as the welding current and the angle of the welding electrode, to ensure proper fusion and prevent excessive melting of the base metal. Use appropriate welding techniques, such as short arc welding, to control the heat input and minimize the occurrence of undercutting.
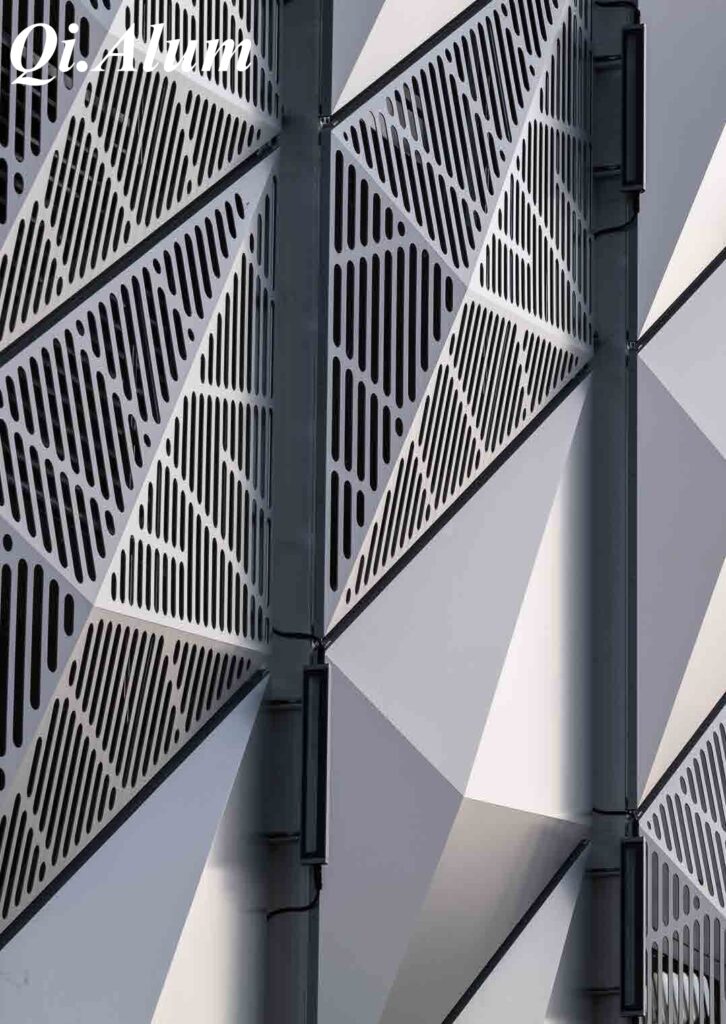
- Problem Description: Weld spatter refers to the small droplets of molten metal that are ejected from the weld pool during the welding process. These spatters can adhere to the surface of the keel and the aluminum single panels, affecting the appearance and potentially causing corrosion if not removed.
- Solutions: Use anti-spatter agents or sprays on the welding surface to reduce the adhesion of spatter. Adjust the welding parameters, such as the welding current and the type of shielding gas, to minimize spatter generation. After welding, carefully remove any spatter particles using appropriate tools, such as wire brushes or grinders.
- Problem Description: Welding deformation occurs when the heat generated during the welding process causes the keel framework to distort or warp. This can lead to difficulties in installing the aluminum single panels and may affect the overall appearance and performance of the exterior wall.
- Solutions: Use appropriate welding sequences and techniques, such as symmetric welding or step-by-step welding, to evenly distribute the heat and minimize deformation. Employ fixtures or clamps to hold the keel in place during welding to restrict movement. If deformation does occur, corrective measures such as mechanical straightening or heat treatment can be applied.
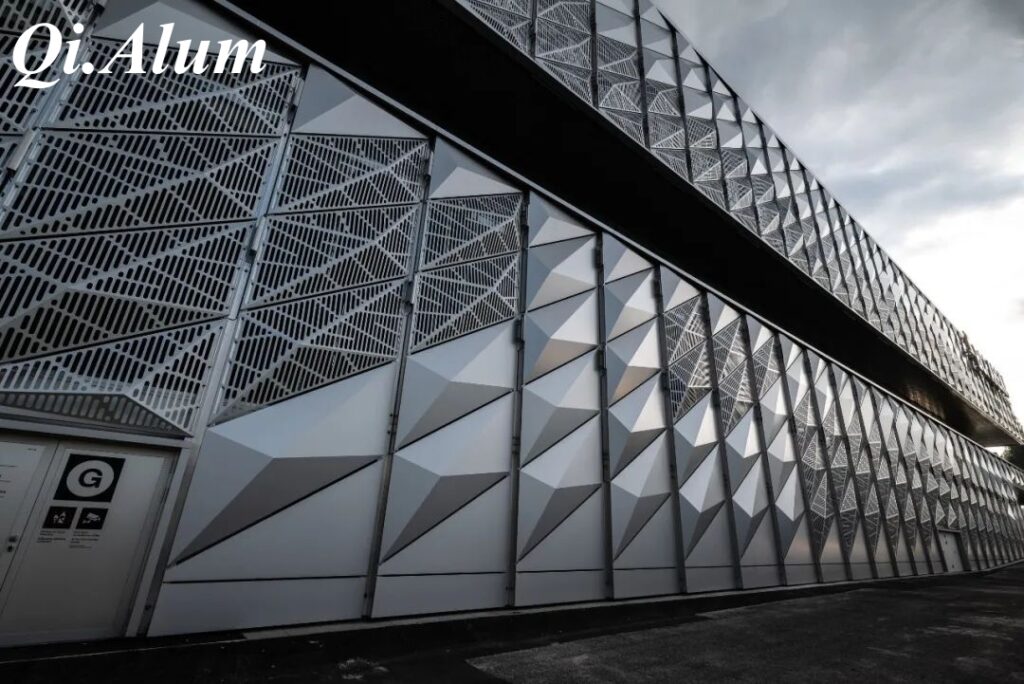
FAQ:
Q:How about customized?
A:Our professional R&D team can meet your OEM/ODM requirement.
Q: How about your quality guarantee ?
A: For all our products, we have certificate and product quality test report.If there is any lost caused by us, we will make compensation.
Q : How about sample ?
A : Free sample can be sent within 5 days after confirmation. But shipping cost will be afford by the buyer, it will be refund when order.
Q : Do you have any successful customer example?
A : Yes, please contact us for more details. And the supplier of Asian City in Guangzhou and Guangzhou Baiyun Airport.
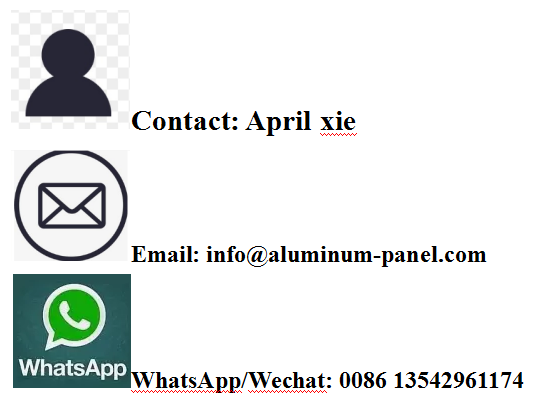
About us:
Foshan Qi Aluminum Decorative Materials Co.,Ltd, more than 12 years experience. We are manufacturer of fabricating aluminum perforated sheets, aluminum solid panels, aluminum screen,aluminum facade decorative sheets, aluminum expanded mesh, aluminum ceiling with good quality and fast delivery for more than 10 years to export countries. Our monthly supplying is about 80000 sqms for inside and outside market. Our projects covers five star hotel, high end villas, school, campus, metro station, airport, office building, shopping mall and some other goverment projects. We can provide design, fabrication and installation one stop service for your projects. High precision, quality guarantee, affordable price, globla delivery and considerate service is our basis. We accept OEM/ODM business. We are the experienced specialist on facade solution decoration!!!
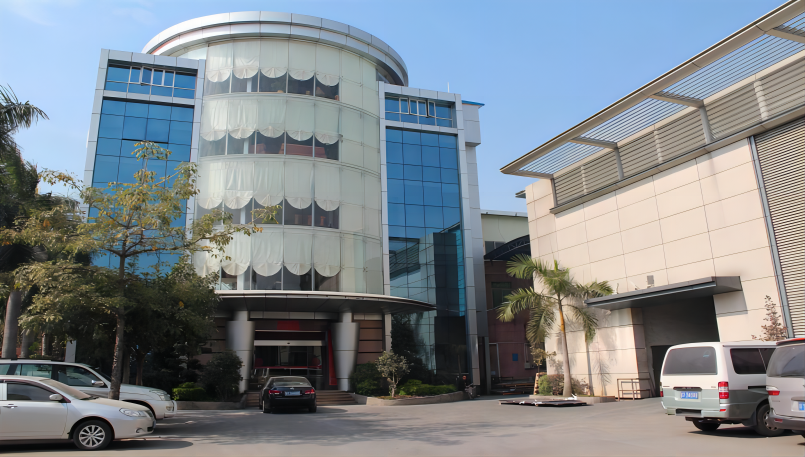