Aluminum veneer metal curtain wall in the second generation of products, aluminum veneer is the use of high-quality aluminum veneer as a substrate, advanced CNC bending technology to ensure that the plate can be formed after processing is not deformed, during the installation of anti-external force Superior performance, the use of fluorocarbon coating on the surface coating, to ensure uniform color surface, anti-ultraviolet radiation, oxidation resistance, super corrosion resistance, the decoration of the building designers want to express the luxurious style or noble and elegant.
So far, aluminum veneer curtain wall decoration only in high-grade cities and high-grade office buildings, landmark building applications, but because of its high cost, so far there is no large-scale use, with China’s rapid economic development, aluminum veneer curtain wall decoration Will be widely used.
According to a number of decorative wall dry hanging aluminum veneer construction experience, summed up in the construction of the skeleton is not vertical, the plate does not match; seams sealant is not dense, varying width; closing connection is not solid, Installation is not meticulous technical quality reasons in three areas, and how to produce the three reasons for the technical quality and processing methods are discussed.
First, the skeleton is not vertical, the board does not match
(A) causes of construction
1. Before the construction, no drawings and interviews will be conducted and the actual site conditions of the construction will be investigated. The workers have not been properly trained and have the technical interview done.
2, the skeleton before the installation, did not measure the actual size of the wall and wall layout, so that the arrangement of the skeleton is not the same distance, the framework of the installation did not measure the flatness, verticality.
3, the framework of drilling did not conduct positioning, the skeleton and the connection between the aluminum plate holes or bolts, pin positions do not coincide with each other.
(B) the main points of quality control and prevention measures
1. Before the start of the whole project, the project manager should organize all the engineers and technicians and the responsible person of the construction operation team to carefully study the design drawings and strengthen the understanding of the drawings. The technical problems appearing in the drawings should be communicated with the Design Institute by the technical manager, Construction quality problems. Construction workers should conscientiously do a good job in technology and safety first, technical explanation must be how to go to the construction of a detailed description of each process, the important processes, parts or links, the appropriate training of workers to improve the technical quality of the implementation of the construction level Method for the whole process of control.
2, before the skeleton installation, due to large errors of civil wall, should be based on the actual situation of the actual measurement of the actual wall size, according to the actual size from the middle to both sides of the symmetrical layout, typesetting map to find Party A, the supervision side confirmation, the pop-up wall positioning Axis and horizontal lines, and then according to the design requirements of the layout of the keel spacing, the elevation of the horizontal line keel grid lines pop up. According to the hanging line, first determine the leftmost, rightmost and middle three embedded parts position, and then pull a horizontal line, in the horizontal line to determine the position of each piece. Determine the location of the embedded parts, according to the buried steel plate at the embedding Department with bold colors to draw its bolt hole location, and then drill with a drill. Anchor hole molding, should be strictly in accordance with the construction process of chemical bolts for construction, the first use of the blowhole blowing out the slag and dust, and then use a dedicated brush East, and then the blow out of the dust, into the kits, with special Appliance into the bolt. When the chemical bolt is to be solidified, put it on the steel plate. After the installation is completed, the elevation deviation should not be greater than 10mm, buried position deviation should not be greater than about 20mm. Should be based on the site pay-off data, strict control of the column material, cross-material processing cuttings size, cutting the material should be adjusted before the finished product, the column deviation should not exceed ± 1mm, horizontal material deviation of not more than ± 0.5 mm; cut ends should not have processing distortion, to avoid burr appear.
3, column installation According to pay-off line to determine the base position, the first connector and column connection, and then connected with the main body embedded parts connected repeatedly adjust the spot welding fixed. Column installation position to be accurate, the elevation of the column installation elevation deviation should not exceed 3mm, before and after the axis deviation of not more than 2mm, left or right deviation of not more than 3mm. Proximity of two vertical column installation elevation deviation is not more than 3mm, the distance between the two adjacent columns deviation of not more than 2mm. The same level of horizontal material installation should be carried out from the bottom up, when the installation of a layer of height should be checked and adjusted, corrected, fixed, so that it meets the design and quality requirements, horizontal material installation of the horizontal elevation deviation should not be greater than 1mm, Stratum height deviation should not be greater than 5mm, both ends of the beam and post fixed 1.5mm expansion joints, fixed after sealing rubber seal. After the column and the crossbeam are installed, the diagonal deviation of each sub-frame should meet the regulatory requirements. When the diagonal is less than or equal to 2 mm, the diagonal difference should be less than or equal to 3 mm; when the diagonal is greater than 2 mm, Angle difference is less than or equal to 3.5mm.
4, aluminum veneer installation, must be in the wall of the pipe, line pipe, noise insulation and other equipment for concealed acceptance, all processes after passing all the acceptance. Check the accuracy of the subdivision grid once it has been tested, whether it has accumulated errors or not. Check whether the size and dimensions of the aluminum single plates are in accordance with the design requirements. Whether the aluminum veneers have the same color, uniform surface, clean, no cracks and defects, Should be promptly adjusted or replaced, there is no problem must be in accordance with the allocation of plate plate location and location of the original bomb in place, with a rivet to fix the aluminum veneer in the vertical keel, first installed from the bottom to the top of the wall, aluminum single The gap between the board and the aluminum veneer is generally 15mm, and then install the doorway, convergence Department, closing treatment. Requires a flat surface, leaving the seam neat, the same size.
Second, seams sealant is not solid, different width
(A) causes of construction
1, in the glue, the silicone sealant is not selected and the use of ordinary sealant.
2, caulking not fully clean the gap between the plates (especially the bonding surface), and to be dried. Polyethylene foam filling depth is inconsistent, when filled with a caulking gun silicone sealant can not form a certain pressure, resulting in poor adhesion and suture, lax sealing.
3, carapace operation unskilled, failed to caulking caulking away from the seams and filling (polyethylene foam filled surface) the same distance, even force, slow squeeze drag, continuous action, resulting in sewn sealant long time less , Joints and more, brought into the air, resulting in seams sealant surface is not straight, a bubble seepage phenomenon.
(B) the main points of quality control and prevention measures
1, use the quality of trustworthy silicone sealant, silicone sealant is always soft, the texture is the same as rubber, ordinary dense, sealing glue will be hardened after drying, a long time will break.
2, Polyethylene foam filling must be tight, should be based on the seam width of the first twist into a slightly thicker than the slit length of the strip and then carefully plugged, and pay attention to fill the surface distance from the board to keep the same depth, not into the out Out Only to maintain the same depth of sealant caulking, clogging behind the back of the state, in order to make dense joints, seam straight.
3, the plastic should pay attention to the temperature above 15 ℃, below 30 ℃, relative humidity above 50%. Caulking gun operation should be sifted when the force size, speed, muzzle filled with polyethylene foam from the surface near the appropriate parameters such as appropriate, should first unobtrusive seams at the test, after the acquisition of mature experience by a straight line, from the From top to bottom, from left to right, once finished. Docking rubs and other individual stitching uneven straight should immediately use hook trowel hook flat. Pay attention to the operating practices, do not let the air enter should be discharged with caulking air discharge, to prevent air bubbles in the event of air bubbles, the use of wire pierced, and immediately with the hook trowel in one direction the air pressure out to seal smooth stop.
Third, closing the connection is not solid, the installation is not detailed
(A) causes of construction
1, before the installation of unfinished design drawings, understand the node structure, drawing design is not reasonable, there is no discussion with the design unit, to deal with, to make the connection firm and adjust its smooth and straight.
2, the installation is not serious blanking and drilling, node structure and connectors do not meet the requirements of the drawings, closing the mouth before not lined, the installation is not detailed, so that the components of the installation error.
(B) the main points of quality control and prevention measures
1, carefully study the design drawings before installation, understand the specific structure of the node, the structure of the local node structure design does not always have reasonable place, and there are improved methods, improved methods will be submitted to the supervision units in writing, the construction units, supervision units and Design units to discuss, with the consent of the design unit can be changed.
2, the installation, the connecting rod must be carefully expected and drilling. Skeleton openings, vents, etc., should be based on the structure of the corresponding node on the drawings set keel and connectors, so that the structure in line with the requirements of the drawings to ensure the rigidity of the skeleton. Before the closing of complicated parts, it should be set out to try to fight, so that the various components can work together without error.
3, in the construction of nodes on the preparation of special construction technology programs to ensure that the correct installation methods, so that the connection between each solid, smooth, sealed, so that the installation process to minimize the error.
Fourth, the board contamination, product protection is not in place
(A) causes of construction
1, After installing the aluminum veneer, there is no one in charge of finished product protection, resulting in the next procedure heavy metal impact aluminum veneer, aluminum veneer surface is not flat or defect.
2, aluminum veneer protection paper removal time too early, but not properly protected, other unfinished construction of its pollution.
(B) the main points of quality control and prevention measures
1, after installation of aluminum veneer, set up a person responsible for the protection of finished products and set up special settings for protection and found damaged protection facilities should be promptly restored. Procedures for the transfer should be fully written in the form, and the two sides signed the endorsement, the next procedure workers to protect the finished product submitted, such as finished product contamination, damage or loss directly responsible for finished product protection negative protection for finished product inspection, inspection responsibility.
2, aluminum veneer surface protection paper should be placed on the project completion or inspection of the near completion of the process can be removed before. After removing the paper, avoid other materials in the transport process of collision aluminum veneer.
3, aluminum veneer and other materials in the transport, approach, storage, use process, should be strictly managed, so that no distortion, no moisture, no rust. Other materials should also be careful not to impact the aluminum veneer wall when sending objects from the door and window openings.
4, once the aluminum veneer surface contaminated, should promptly use a clean cotton sand (not sand folder) to scrub it clean.
Fifth, the conclusion
Aluminum veneer due to higher cost, not widely used at this stage, but with the rapid economic development in our country, aluminum veneer curtain wall decoration will be widely used. Aluminum veneer is generally used to install the skeleton, carefully study the design drawings before installation, understand the specific structure, installation, the connecting rod must be carefully blanking and drilling, so that the various components can be coordinated with each other. In the meantime, a proper installation method should be established. In particular, measures should be taken to make it easy to adjust the various installation errors. In the construction process should pay attention to: 1. Skeleton is not vertical, the board does not match; 2. seams sealant is not dense, varying width; 3. shut connection is not solid, installation is not detailed; 4. also pay attention to finished product protection , After delivery to tear off the plastic protective film to prevent surface contamination, hit a dent.
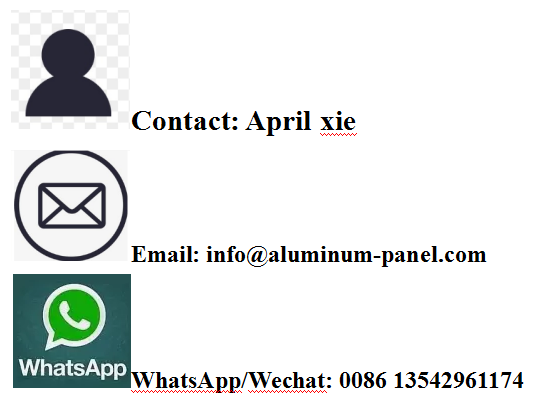