Processing process: aluminum to the oil decontamination → washing → washing (degreasing) → washing → pickling → washing → washing → washing → washing → pure water to wash fluorocarbon spraying process: spray primer → finish paint → paint Baked (180-250 ℃) → quality inspection
Multi-layer fluorocarbon coating process to three spray (referred to as three spray), spray the bottom paint, paint and varnish and secondary spray (primer, topcoat).
1. The purpose of pre-treatment: aluminum alloy profiles, sheet metal before the fluorocarbon coating, the workpiece surface to go through the oil decontamination and chemical treatment to produce chrome film, increase the coating and metal surface adhesion and oxidation resistance, Is conducive to extend the life of the paint film.
2. Primer coating: as a closed substrate primer coating, its role is to improve the coating anti-permeability, and enhance the protection of the substrate, stabilize the metal surface layer, strengthen the topcoat and metal surface adhesion, To ensure that the paint coat color uniformity, paint layer thickness is generally 5-10 microns.
3. Topcoat: Topcoat coating is a key layer of fluorocarbon coating, is to provide the necessary decorative colors of aluminum, aluminum appearance to meet the design requirements, and to protect the metal surface from the outside world atmosphere, acid rain , Pollution of the erosion, to prevent UV penetration. Greatly enhance the anti-aging ability, topcoat coating is the thickest layer of fluorocarbon coating, paint layer thickness is generally 23-30 microns.
4. Lacquered paint coating: gloss paint coating, also known as varnish coating, the main purpose is to more effectively enhance the paint layer against the outside world, the ability to protect the finish, increase the finish color of metallic luster, the appearance of more color Bright, dazzling, coating thickness is generally 5-10 microns. The total thickness of the fluorocarbon coating is generally 40-60 microns, the special needs can be thickened.
5. Curing treatment: PTFE spray coating generally need secondary curing, aluminum into the curing furnace treatment, curing temperature is generally between 180 ℃ -250 ℃, curing time of 15-25 minutes, different fluorocarbon coating manufacturers, Will be based on their own paint, to provide the best temperature and time. Fluorocarbon spraying plant (or refinery) and some according to their own experience to three times when the two curing to a curing.
6. Quality inspection: quality inspection should be AAMA-605.02.90 standard. Strict quality inspection to ensure high-quality spray products.
Single-layer aluminum veneer is widely used in building curtain wall, its surface PVDF fluorocarbon coating is usually formed by spraying process, but also by roller coating process. The former is the first through the sheet metal processing technology to the processing of aluminum into a stiffener and the structure of the ear, and then PVDF fluorocarbon spraying. The roller plate is first by roller coating process in the aluminum plate surface roller coating PVDF fluorocarbon spraying, and then through the sheet metal processing technology to the coating plate into a certain structure. In this paper, the difference between application and performance of spray plate and roller coating in curtain wall is compared and analyzed.
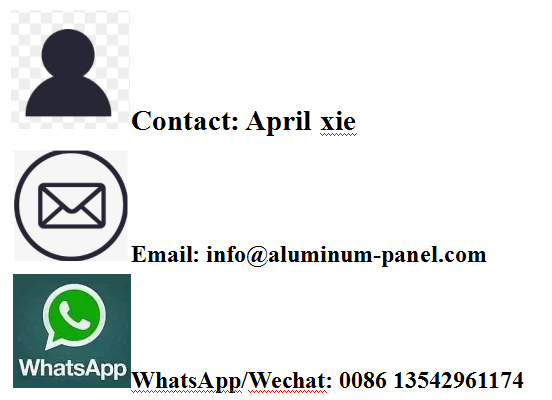