Aluminum single – layer panels are made entirely of aluminum alloy. High – quality aluminum alloys, such as 3003 or 5005 series, are commonly used. These alloys endow the panels with excellent strength, durability, and corrosion resistance. The aluminum thickness usually ranges from 1.5mm to 5mm, depending on the application requirements. For instance, in high – rise building curtain walls, thicker panels around 3 – 5mm might be chosen to withstand strong winds and external forces.
Aluminum composite panels consist of two thin aluminum sheets bonded to a non – aluminum core material. The outer aluminum layers are typically 0.1 – 0.5mm thick, while the core can be made of materials like polyethylene (PE), fire – resistant mineral – filled polyethylene, or polyurethane. The core provides insulation and lightweight properties, making the overall panel more cost – effective for certain applications. For example, in interior decoration projects where fire – resistance is not the most critical factor, PE – cored aluminum composite panels are often used.
Aluminum ceiling panels are usually made of relatively thin aluminum sheets, commonly with a thickness of 0.4 – 1.2mm. They are often made from pure aluminum or low – alloy aluminum. Some aluminum ceiling panels may also be pre – coated with various finishes for better aesthetics and corrosion resistance. The choice of alloy and thickness depends on the specific requirements of the ceiling installation, such as load – bearing capacity and appearance.
These panels offer a wide range of surface finish options. They can be powder – coated, fluorocarbon – coated, anodized, or brushed. Fluorocarbon coating, in particular, is highly popular for exterior applications due to its excellent weather resistance and color – retention properties. The smooth and flat surface of aluminum single – layer panels can create a high – end and modern look, suitable for large – scale commercial buildings and high – end residential projects.
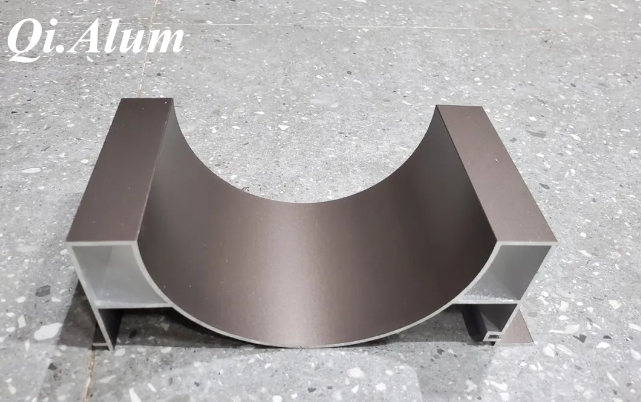
Aluminum composite panels also come with diverse surface finishes. Powder coating and fluorocarbon coating are common choices. However, compared to aluminum single – layer panels, the surface of aluminum composite panels may have a slightly different texture due to the sandwich structure. They are often used in projects where a cost – effective yet aesthetically pleasing finish is required, such as shopping malls and office buildings.
Aluminum ceiling panels usually have a more decorative surface finish. They can be printed with various patterns, textures, or colors to match different interior design styles. Some may have a matte finish for a soft and elegant look, while others may have a glossy finish to add a touch of luxury. Additionally, some aluminum ceiling panels are designed with perforations for acoustic purposes.
- Aluminum Single – layer Panels: With their solid aluminum structure, they have high strength and rigidity. They can withstand significant external loads, making them suitable for applications like curtain walls in high – rise buildings. Their ability to maintain shape and integrity over time is excellent, even in harsh weather conditions.
- Aluminum Composite Panels: While they offer good strength for many applications, their strength is relatively lower compared to aluminum single – layer panels due to the presence of the non – aluminum core. However, for most interior and some low – rise exterior applications, their strength is sufficient. The sandwich structure provides some flexibility, which can be an advantage in certain situations.
- Aluminum Ceiling Panels: Designed mainly for ceiling applications, they have adequate strength to support their own weight and any additional light fixtures or insulation materials. Their rigidity is tailored to meet the requirements of ceiling installation, ensuring a flat and stable appearance.
- Aluminum Single – layer Panels: Aluminum itself is non – combustible. However, the surface finish, such as the coating, may have different fire – resistance ratings. High – quality fluorocarbon coatings can have good fire – resistant properties, and in some cases, additional fire – retardant treatments can be applied to meet specific fire – safety standards.
- Aluminum Composite Panels: The fire resistance of aluminum composite panels depends largely on the core material. PE – cored panels have relatively poor fire resistance, while fire – resistant mineral – filled polyethylene or other fire – retardant cores can significantly improve their fire – rating. In some areas with strict fire – safety regulations, only fire – resistant aluminum composite panels are allowed for certain applications.
- Aluminum Ceiling Panels: Similar to aluminum single – layer panels, their fire resistance is mainly determined by the surface finish and any additional fire – retardant treatments. Some aluminum ceiling panels are designed specifically to meet high fire – safety standards, especially in public buildings.
- Aluminum Single – layer Panels: With proper surface treatment, especially fluorocarbon coating, aluminum single – layer panels exhibit excellent weather resistance. They can resist UV radiation, rain, and atmospheric pollutants for long periods without significant fading, corrosion, or degradation. This makes them ideal for long – term exterior applications.
- Aluminum Composite Panels: Although they also have some degree of weather resistance, the performance may be slightly inferior to aluminum single – layer panels, especially in extremely harsh weather conditions. The bonding between the aluminum sheets and the core may be affected over time by temperature changes, humidity, and UV exposure.
- Aluminum Ceiling Panels: Since they are mostly used indoors, weather resistance is not a major concern. However, for outdoor – exposed ceilings or in humid indoor environments, they still need to have a certain level of corrosion resistance to ensure a long service life.
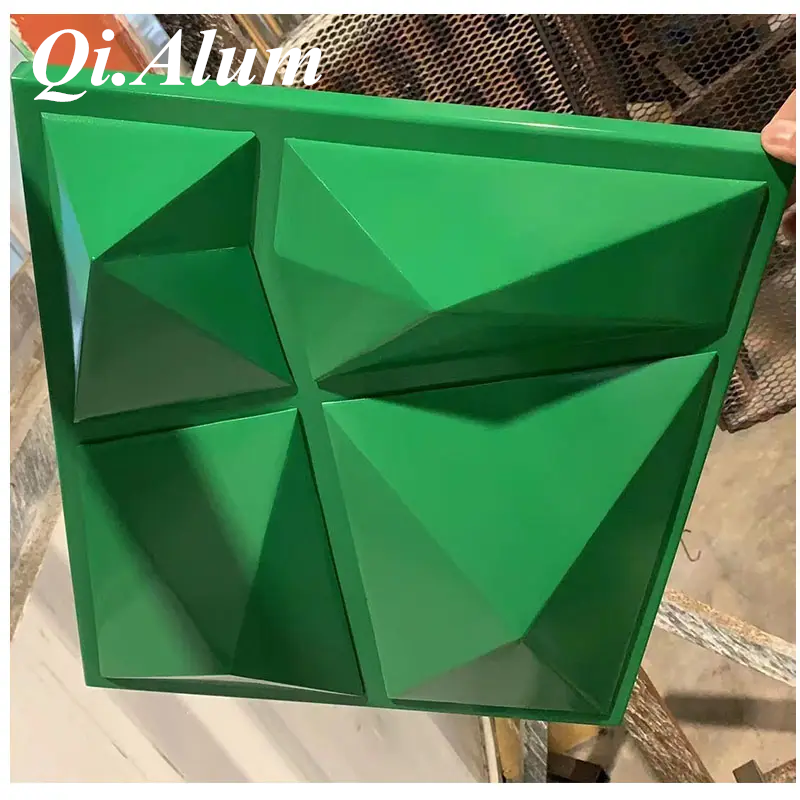
- Exterior Curtain Walls: Their high strength, weather resistance, and aesthetic appeal make them a top choice for high – rise building curtain walls. They can create a sleek and modern exterior facade, and their durability ensures a long – lasting appearance.
- Large – scale Commercial Buildings: Such as exhibition centers, airports, and shopping malls. The large – format aluminum single – layer panels can be customized to fit the unique architectural design requirements of these buildings.
- Interior Decoration: They are widely used for interior wall cladding, partition walls, and suspended ceilings in commercial and residential buildings. Their lightweight and cost – effectiveness, combined with good aesthetic options, make them popular for interior design projects.
- Low – rise Building Exteriors: In some low – rise buildings or renovation projects where cost is a major consideration, aluminum composite panels can be used for exterior facades to achieve a good visual effect at a relatively lower cost.
- Residential and Commercial Ceilings: They are the primary choice for both residential and commercial ceiling installations. Their decorative surface finishes and ease of installation make them suitable for creating various ceiling styles, from simple and modern to more elaborate and decorative.
- Acoustic Ceiling Applications: Some perforated aluminum ceiling panels are used in spaces where acoustic performance is important, such as auditoriums, conference rooms, and classrooms.